Avances en el mantenimiento de la minería subterránea mediante la digitalización y la automatización
Publicado hace 9 meses
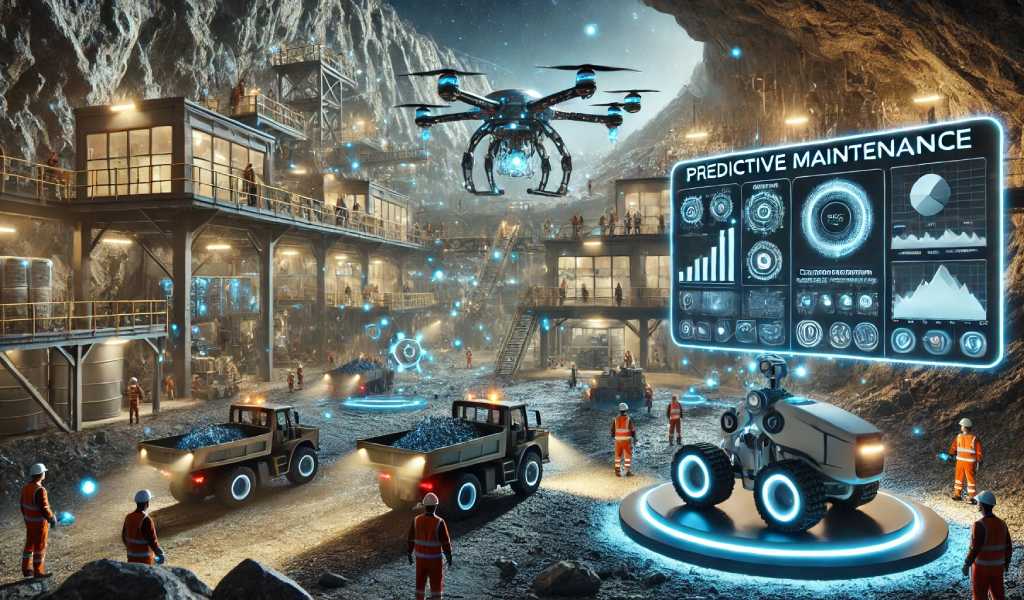
Los recientes avances en estas temáticas ofrecen ahora un potencial transformador para las estrategias de mantenimiento en la minería subterránea.
La minería subterránea, esencial para el abastecimiento mundial de materias primas, y especialmente para la mayoría de las materias primas críticas, se enfrenta a importantes retos, como la seguridad de los trabajadores, la eficiencia operativa y la sostenibilidad medioambiental.
Tradicionalmente, las estrategias de mantenimiento en este sector se basaban en gran medida en inspecciones manuales y programas de mantenimiento preventivo basados en el tiempo. Sin embargo, estos enfoques convencionales han resultado a menudo laboriosos, costosos e insuficientes para predecir o prevenir eficazmente los fallos de los equipos. Los recientes avances en digitalización y automatización -específicamente a través de la monitorización del estado, el mantenimiento predictivo y las inspecciones automatizadas- ofrecen ahora un potencial transformador para las estrategias de mantenimiento en la minería subterránea, abordando los principales retos de la industria.
Limitaciones del mantenimiento tradicional en minería
Durante décadas, el mantenimiento de la minería subterránea ha dependido de inspecciones manuales y programas de mantenimiento predeterminados, en los que las revisiones de los equipos se realizaban a intervalos fijos, independientemente de su estado real.
Aunque útiles, estas medidas preventivas basadas en el tiempo son intrínsecamente limitadas, y a menudo conducen a tareas de mantenimiento innecesarias o, por el contrario, a fallos inesperados de los equipos. Por ejemplo, el personal cualificado realiza comprobaciones periódicas basándose en la experiencia y el juicio, lo que puede dar lugar a incoherencias y a la posibilidad de pasar por alto alertas tempranas de problemas en los equipos.
Además, el mantenimiento tradicional requiere muchos recursos, lo que implica un trabajo manual considerable en entornos subterráneos peligrosos, lo que aumenta los riesgos de seguridad y los costes operativos
Digitalización y automatización
Durante los últimos 15 años, el cambio continuo hacia soluciones digitalizadas y automatizadas en el mantenimiento marca una evolución fundamental en la minería subterránea. La monitorización de las condiciones, el mantenimiento predictivo y los sistemas de inspección automatizados aportan ventajas específicas a la hora de mejorar la eficiencia y la fiabilidad operativas.
La implantación de la monitorización de estado permite recopilar datos en tiempo real sobre los parámetros de los equipos, como la temperatura, la vibración y la presión, a través de redes de sensores. Mediante el análisis de estos datos, los operadores mineros pueden determinar con precisión las necesidades de mantenimiento de la maquinaria, en lugar de depender de calendarios inflexibles. Por ejemplo, en una mina subterránea sudafricana, la aplicación de este método supuso una reducción del 30% de los tiempos de inactividad, lo que ofrece claras ventajas para un funcionamiento fiable e ininterrumpido.
A partir de ahí, el mantenimiento predictivo aplica algoritmos avanzados de aprendizaje automático para prever los fallos de la maquinaria antes de que se produzcan, con lo que el mantenimiento pasa de ser reactivo a proactivo. Al anticiparse a los problemas de los equipos, el mantenimiento predictivo reduce la necesidad de reparaciones de emergencia y limita la exposición del personal en zonas de alto riesgo. Los estudios han demostrado que el mantenimiento predictivo puede reducir el tiempo de inactividad de la maquinaria hasta en un 20%, al tiempo que mejora los niveles de seguridad.
En un caso notable, una explotación minera que utilizaba algoritmos de mantenimiento predictivo experimentó un descenso significativo de las interrupciones operativas, lo que ilustra el potencial del mantenimiento basado en datos en entornos de alto riesgo como la minería subterránea.
Uno de los avances más recientes son los sistemas de inspección automatizados, incluidos los drones y la robótica, que permiten realizar inspecciones en zonas peligrosas o de difícil acceso sin necesidad de intervención humana directa. Los drones, equipados con cámaras de alta resolución y otros sensores, realizan inspecciones rutinarias con una rapidez y precisión excepcionales, lo que contribuye a reducir los tiempos de inspección y a mejorar la precisión de los datos. Una empresa minera, por ejemplo, consiguió reducir en un 50% el tiempo de inspección tras utilizar drones para las comprobaciones periódicas de los equipos, lo que pone de manifiesto las mejoras de eficiencia y seguridad que se pueden conseguir con la automatización.
Ventajas y sostenibilidad de las estrategias de mantenimiento digitalizadas
La implantación de estrategias de mantenimiento digitalizadas y automatizadas ofrece claras ventajas en cuanto a seguridad, eficiencia y sostenibilidad. La mejora de la seguridad es uno de los principales resultados, ya que las herramientas digitales y automatizadas reducen la necesidad de que el personal realice inspecciones en zonas peligrosas, lo que disminuye los índices de accidentes asociados a las comprobaciones manuales tradicionales. El aumento de la eficiencia es igualmente significativo: con una programación precisa del mantenimiento facilitada por el análisis de datos, las empresas minimizan los tiempos de inactividad innecesarios y maximizan la vida útil de la maquinaria. Además, este enfoque contribuye a reducir costes, ya que el mantenimiento predictivo y el basado en el estado reducen tanto los costes de las reparaciones de emergencia como los gastos a largo plazo de la sustitución de equipos.
Desde el punto de vista de la sostenibilidad, los modelos de mantenimiento automatizado y predictivo contribuyen directamente a la conservación de los recursos. La reducción de la frecuencia de mantenimiento y la mejora de la eficiencia operativa reducen el consumo de energía y los residuos de materiales, en consonancia con los principios de la economía circular. Las inspecciones automatizadas y los modelos predictivos fomentan una explotación minera más respetuosa con el medio ambiente al reducir las emisiones de carbono y minimizar la producción de residuos, lo que es cada vez más importante para un sector sometido a presiones para cumplir estrictas normas medioambientales.
Fuente: Tecnología Minera

TAMBIÉN TE PUEDE INTERESAR
La convergencia de la ciberseguridad, el cumplimiento normativo y los . . .
22/Aug/2025 4:47pm
La gestión de riesgos empresariales está entrando en una nueva fase en la que la ciberseguridad, el cumplimiento norma . . .
Ministro Hales innova en el control de emisiones con aditivo sustentab . . .
22/Aug/2025 4:46pm
La aplicación de este aditivo orgánico permite alcanzar un 95% de eficiencia en la mitigación de polvo por el tránsi . . .
Huawei impulsa la mayor flota de camiones autónomos del mundo . . .
22/Aug/2025 4:45pm
La industria minera en China acaba de marcar un hito en automatización. El grupo energético estatal Huaneng presentó . . .
Perú cuenta con 10 centrales eólicas de generación, con una potenci . . .
22/Aug/2025 4:39pm
Parques eólicos se ubican en la costa y sierra del país, que cuenta con un potencial de 20 GW para futuros proyectos. . . .
Suscríbete al Boletín
Para recibir noticias diarias de Tecnología Minera