Optimización de la eficiencia energética en la fabricación con Condition Monitoring
Publicado hace 3 meses
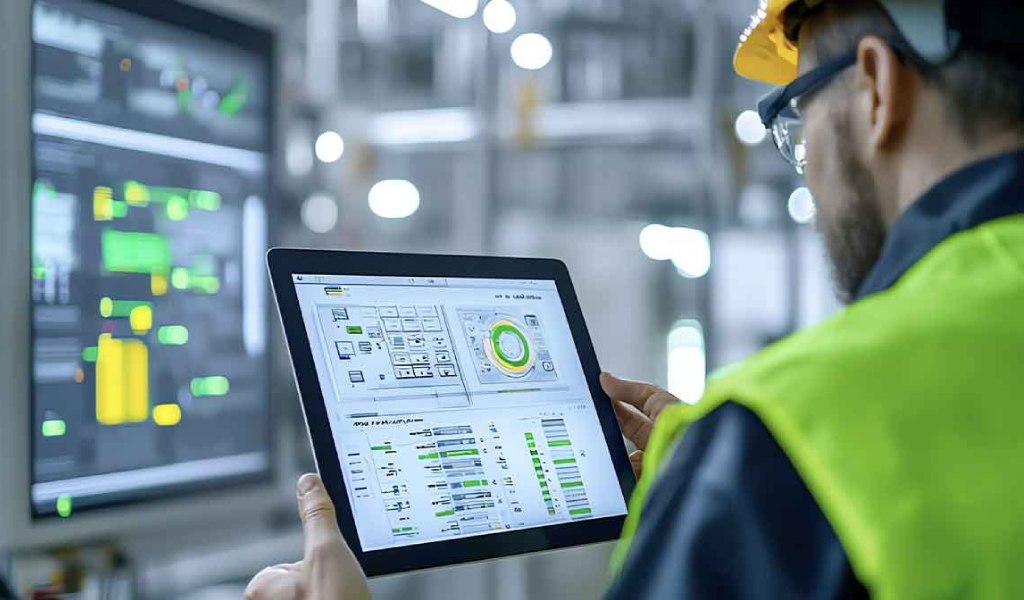
En el competitivo panorama actual de la fabricación, la eficiencia operativa y la sostenibilidad son esenciales para el éxito a largo plazo.
Los motores industriales, que alimentan los procesos de fabricación, representan casi el 60% de todo el consumo de energía eléctrica. Sin embargo, las ineficiencias como la desalineación, el desgaste y el funcionamiento incorrecto conducen a un desperdicio excesivo de energía, lo que aumenta los costes y el impacto medioambiental.
El papel de la monitorización de estado en la optimización energética
La monitorización de estado utiliza técnicas de diagnóstico no invasivas como el análisis de vibraciones, la termografía infrarroja y el análisis de datos basado en IA para detectar ineficiencias en los motores industriales antes de que se conviertan en averías graves. Este enfoque proactivo permite a los fabricantes
- Reducir el tiempo de inactividad mediante la prevención de averías inesperadas de los equipos.
- Optimizar el consumo de energía mediante la supervisión del rendimiento en tiempo real.
- Prolongar la vida útil de los equipos garantizando que los motores funcionen con la máxima eficiencia.
- Reducir los costes operativos minimizando los residuos y el mantenimiento innecesario.
Implementación de Condition Monitoring para obtener el máximo impacto
Para maximizar la eficiencia energética, los fabricantes deben seguir un enfoque estructurado:
- Identificar los equipos críticos - Centrarse en la maquinaria de alto impacto con el mayor consumo de energía.
- Seleccionar la tecnología de monitorización adecuada - Utilizar sensores y análisis basados en IA para detectar ineficiencias.
- Asegurar la colocación estratégica de los sensores - Colocar los sensores para obtener datos precisos en tiempo real.
- Supervise continuamente el rendimiento - Haga un seguimiento de las anomalías y las fluctuaciones energéticas.
- Actúe a partir de la información: aborde las ineficiencias antes de que provoquen un aumento de los costes o fallos.
Impacto en el mundo real: Ahorro de energía en empresas de suministro de agua
Una importante empresa de suministro de agua del Reino Unido implantó la monitorización de estado en más de 300 estaciones de bombeo. Los análisis basados en IA identificaron un problema de resonancia en una bomba de velocidad variable, que provocaba un consumo excesivo de energía. Al detectar el problema a tiempo, la empresa optimizó el uso de energía, reduciendo costes y mejorando la fiabilidad de la infraestructura.
Los avances en IoT, IA y análisis predictivo están revolucionando las estrategias de mantenimiento. Mediante la integración de soluciones de supervisión inteligentes, los fabricantes pueden mejorar la eficiencia energética, la fiabilidad de los equipos y los objetivos de sostenibilidad.
Fuente: Tecnología Minera

TAMBIÉN TE PUEDE INTERESAR
Tecnominproductos: Soluciones Integrales para Minería, Energía e Ind . . .
14/Aug/2025 9:07am
En sectores tan exigentes como la minería, la energía y la industria, la disponibilidad de insumos confiables no es un . . .
Gestión de riesgos geotécnicos en minería subterránea: Prevención . . .
13/Aug/2025 4:35pm
Descubre las herramientas y protocolos clave para prevenir deslizamientos, hundimientos y fallas estructurales en miner . . .
Impulsan la conectividad minera con nuevos corredores de alta capacida . . .
13/Aug/2025 4:32pm
La nueva infraestructura enfocada en corredores mineros en Arequipa permitirá mejorar la calidad y cobertura de los ser . . .
Argentina: Argenta Silver anuncia hallazgo récord de plata de alta le . . .
13/Aug/2025 4:29pm
Argenta Silver Corp. anuncia resultados excepcionales en su proyecto El Quevar, Salta. Se halló plata de alta ley, con . . .
Suscríbete al Boletín
Para recibir noticias diarias de Tecnología Minera