Conoce las tecnologías que permiten automatizar los cargadores de bajo perfil
Publicado hace 1 año
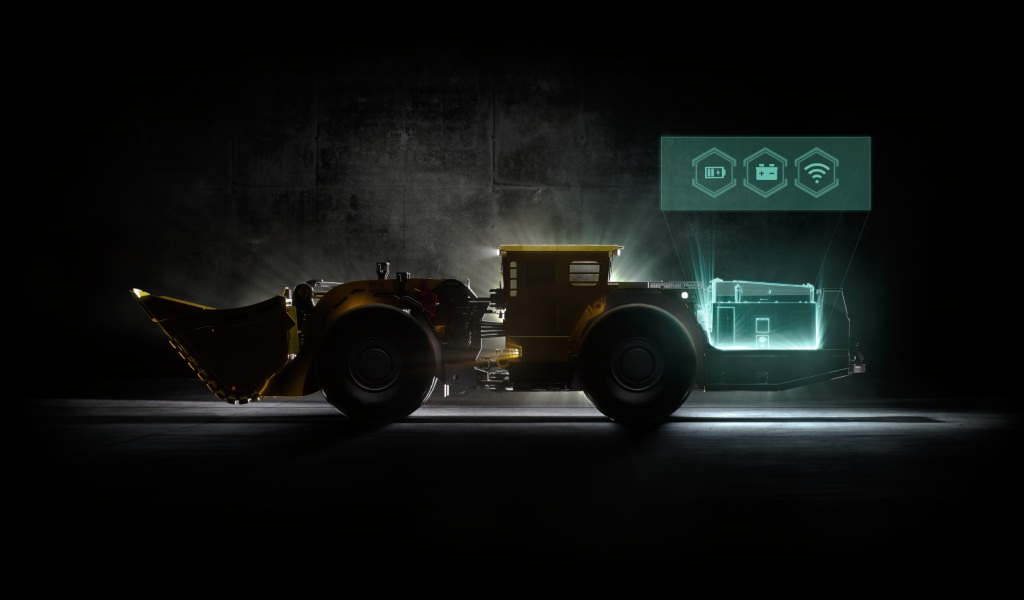
Cabe mencionar que todos estos sistemas de automatización se comunican mediante una red de comunicación Wifi por lo que es necesario contar con señal de internet en todo el túnel por donde recorren los equipos.
La minería, como la mayoría de sectores en el país, tienen como objetivo común encontrar la mayor rentabilidad posible en sus operaciones, por ello, contar con equipos y maquinarias que permitan agilizar el proceso es una ventaja competitiva que resalta a gran escala.
En ese sentido, los cargadores de bajo perfil o también conocidos como cargadores para minería subterránea, son un gran aliado para las compañías mineras por los diversos beneficios que brinda dentro de un espacio reducido, poco amigable y peligroso para un ser humano.
Debido a las condiciones de trabajo en las cuales se desempeñan, los cargadores de bajo perfil cuentan con características específicas adaptadas a las condiciones del socavón. En ese sentido, estos equipos deben ser compactos y potentes, para poder operar en áreas de trabajo reducidas y en rampas inclinadas de manera eficiente.
Para optimizar el funcionamiento de los cargadores de bajo perfil, es importante reconocer para qué trabajo específico se necesitará el equipo y así saber los distintos grados de autonomía en función a los opcionales que otorga el proveedor.
Así lo señala, Santiago Arenas, gerente de la División Subterránea de Epiroc Perú, quien afirmó que “estos equipos pueden ser operados directamente por el operador en cabina, también pueden ser utilizados a través de una línea de radio control remoto o a través de una operación teleremota a distancia y finalmente, totalmente autónomos sin la intervención de los operadores, programados para trabajar en rutas predeterminadas”.
En ese sentido, Ferreyros, a través de Caterpillar, cuenta con una amplia gama de herramientas de automatización que optimizan el funcionamiento de los cargadores de bajo perfil, en este caso, aquellos equipos desde 10 tn, que se encuentran equipados con la tecnología MineStar Command for Underground de Caterpillar, y que pueden operar de manera completamente autónoma en el ciclo de acarreo y descarga, así como el proceso de carga. Esta tecnología es operada desde una estación de control fija ubicada en una zona segura dentro del socavón.
Esta destacada innovación ofrece soluciones escalables adaptadas a necesidades específicas de cada operación, que van desde la operación remota de equipos dentro de la línea de vista hasta la autonomía total del ciclo completo de carguío y acarreo.
“Todo esto es posible gracias a los módulos Teleremote (operación remota desde una estación central), Copilot (autonomía en acarreo y operación remota para carguío y descarga), Autopilot (autonomía en acarreo y operación remota para carga) y Autonomy (capacidad de operación 100% autónoma)”, señalan desde Ferreyros.
Esta tecnología, que incorpora sistemas de automatización a bordo de la máquina, como cámaras, radares y sensores, también incluye un centro de control desde el cual se pueden configurar los parámetros de operación de la máquina y operar los equipos de forma remota. A su vez, cuenta con una red de radio de área local que facilita la comunicación entre el centro de control y el cargador de bajo perfil, y un sistema de aislamiento de área que delimita la zona en la que las máquinas autónomas pueden operar.
Por su parte, Luis Campos, Ingeniero de Aplicaciones de Sandvik Perú, destaca la propuesta que ofrece la empresa a través de AutoMine®.
“AutoMine® ofrece una amplia variedad de opciones de automatización tales como: Lite, Multi-Lite y Fleet. Las diferencias entre estos sistemas radican, principalmente, en la complejidad de su tecnología y en la cantidad de equipos que se pueden automatizar, partiendo desde la automatización de un solo equipo hasta la automatización de una flota completa de cargadores y camiones”, señaló Campos.
Cabe mencionar que todos estos sistemas de automatización se comunican mediante una red de comunicación Wifi por lo que es necesario contar con señal de internet en todo el túnel por donde recorren los equipos.
De esta forma, las ventajas de un cargador de bajo perfil se maximizan en relación a la seguridad, pues ya no es necesaria la presencia de un operador dentro del equipo, erradicando así la pérdida humana ocasionada por un accidente o colisión de territorios. Asimismo, se incrementa la productividad del equipo significativamente debido a que el sistema optimiza al máximo el traslado del material lo que hace más eficiente el ciclo de carguío y acarreo del cargador.
Fuente: Tecnología Minera

TAMBIÉN TE PUEDE INTERESAR
Biotecnología en minería: bacterias y enzimas para recuperación sos . . .
29/Aug/2025 4:33pm
Descubre cómo la biotecnología aplicada a la minería utiliza bacterias y enzimas para recuperar metales de forma sost . . .
Innovación en minería: Soluciones para manejo de materiales en miner . . .
29/Aug/2025 4:28pm
Descubre la evolución de las soluciones para manejo de materiales en minería: tecnologías resistentes, mayor producti . . .
México: Luca Mining expande mina Tahuehueto en un 25 % . . .
29/Aug/2025 4:23pm
Luca Mining adquiere la concesión Humaya 3 de Fresnillo en Durango, expandiendo en 25% su mina Tahuehueto, que ya produ . . .
PERUMIN Hub: “Jóvenes que transforman” bate récord y recibe 117 . . .
29/Aug/2025 4:22pm
El presidente del Comité Organizador, Rafael Estrada, resaltó que en la categoría internacional se recibieron propues . . .
Suscríbete al Boletín
Para recibir noticias diarias de Tecnología Minera