Mantenimiento de maquinaria minera: Estrategias para reducir tiempos de inactividad
Publicado hace 5 meses
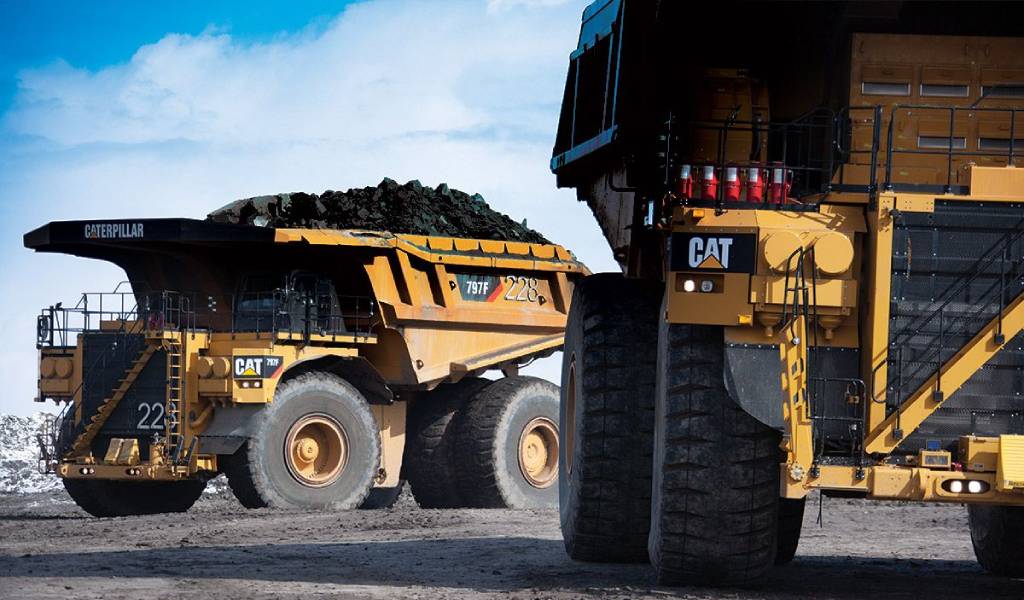
La adopción de estrategias como el mantenimiento predictivo y la digitalización de procesos es esencial para reducir los tiempos de inactividad en la maquinaria minera.
En la industria minera, la eficiencia operativa es fundamental para garantizar la rentabilidad y sostenibilidad de las operaciones. Uno de los desafíos más significativos es minimizar los tiempos de inactividad de la maquinaria, que pueden generar pérdidas económicas considerables. Para abordar este reto, diversas estrategias de mantenimiento han sido implementadas con éxito en el sector, destacando el mantenimiento predictivo como una de las más efectivas.
El mantenimiento predictivo se basa en la monitorización continua de los equipos mediante sensores y el análisis de datos en tiempo real. Esta metodología permite anticipar fallos potenciales antes de que ocurran, facilitando la planificación de intervenciones y evitando paradas inesperadas. La adopción de esta estrategia no solo mejora la disponibilidad de la maquinaria, sino que también optimiza los costos operativos y prolonga la vida útil de los activos.
Un ejemplo destacado es el de Codelco en Chile, uno de los mayores productores de cobre a nivel mundial. La empresa implementó un sistema de mantenimiento predictivo que le permitió reducir en un 15% las paradas no programadas de sus equipos mineros. Esta iniciativa no solo optimizó las operaciones, sino que también contribuyó a la reducción del consumo energético y las emisiones de CO2, alineándose con sus objetivos de sostenibilidad.
En Australia, la multinacional Rio Tinto adoptó tecnologías avanzadas de mantenimiento predictivo en sus minas de mineral de hierro. Al integrar inteligencia artificial y aprendizaje automático en sus procesos, la compañía logró una disminución del 30% en los costos de mantenimiento y extendió la vida útil de sus equipos en un 20%. Estos avances fueron cruciales para mantener su competitividad en un mercado con márgenes de ganancia cada vez más ajustados.
Por su parte, Vale, el mayor productor de hierro del mundo, implementó un sistema de mantenimiento predictivo en su mina de Carajás, la mayor mina de hierro a cielo abierto. Gracias a la monitorización continua y al análisis predictivo, la compañía logró reducir en un 25% el tiempo de inactividad de los equipos críticos, manteniendo altos niveles de producción y cumpliendo con sus compromisos de suministro, incluso en épocas de alta demanda.
En Sudáfrica, Anglo American aplicó un sistema de mantenimiento predictivo en su mina de platino, utilizando herramientas avanzadas de análisis y sensores en sus equipos. Este enfoque permitió detectar fallos potenciales semanas antes de que ocurrieran, facilitando la programación de mantenimientos preventivos sin interrumpir la producción. Como resultado, la compañía redujo los costos operativos en un 20% y mejoró la seguridad, minimizando el riesgo de accidentes.
Otra estrategia innovadora es la digitalización de los procesos de mantenimiento. Empresas como Value Hybrid han desarrollado plataformas que optimizan y aseguran los procedimientos de bloqueo y etiquetado en el mantenimiento de maquinaria industrial. Su herramienta Value Digital Loto digitaliza el proceso LockOut/TagOut (Loto), garantizando que los pasos se sigan correctamente y eliminando el riesgo de omisiones. Esta solución ha resultado en un ahorro de tiempo en mantenimiento de entre 20% y 40% y ha mejorado la gestión de registros.
Asimismo, la empresa Fracttal se dedica a la digitalización del mantenimiento en diversas industrias, incluida la minera. Su tecnología permite mantener los activos en óptimas condiciones, previniendo fallos y resolviendo problemas antes de que ocurran. La herramienta incluye un software de organización y planificación, soluciones de IoT para alertas en tiempo real y programas de mantenimiento preventivo. Esta digitalización ha contribuido a una mayor eficiencia operativa y a la reducción de tiempos de inactividad.
La implementación de estas estrategias requiere una inversión inicial en tecnología y capacitación del personal. Sin embargo, los beneficios a largo plazo, como la reducción de costos, la mejora en la seguridad y el aumento de la productividad, justifican ampliamente la adopción de estas prácticas. Además, al minimizar las interrupciones en la operación, las empresas pueden cumplir de manera más efectiva con sus compromisos de producción y fortalecer su posición en el mercado.
En conclusión, la adopción de estrategias como el mantenimiento predictivo y la digitalización de procesos es esencial para reducir los tiempos de inactividad en la maquinaria minera. Estos enfoques permiten anticipar y prevenir fallos, optimizar recursos y mejorar la eficiencia operativa. Los casos de éxito en la industria demuestran que invertir en estas tecnologías es una decisión estratégica que contribuye al crecimiento sostenible y a la competitividad de las empresas mineras en un entorno global cada vez más exigente.
Fuente: Tecnología Minera

TAMBIÉN TE PUEDE INTERESAR
De qué manera los fabricantes pueden aprovechar el 100 % de los datos . . .
15/Aug/2025 5:22pm
Cuando los datos maestros de los activos carecen de calidad, hasta el 90 % de la información generada por el IoT en la . . .
Transporte y manejo de materiales en minería: Eficiencia, continuidad . . .
15/Aug/2025 5:18pm
Descubre cómo la automatización, la analítica avanzada y las nuevas tecnologías optimizan el transporte y manejo de . . .
Anuncian la construcción de una fundición futurista en Perú . . .
15/Aug/2025 5:05pm
Bradken ha anunciado que su filial con sede en Perú ha iniciado la construcción de su nueva fundición, eficiente desd . . .
Slope Stability 2026: La estimación de parámetros geotécnicos son v . . .
15/Aug/2025 5:03pm
Esos estudios permiten conocer las características del terreno para las excavaciones, minimizar riesgos y garantizar la . . .
Suscríbete al Boletín
Para recibir noticias diarias de Tecnología Minera