Auto-limpieza, auto-calibración y totalmente automatizado: retroalimentación de fluidos de la Industria 4.0
Publicado hace 5 años
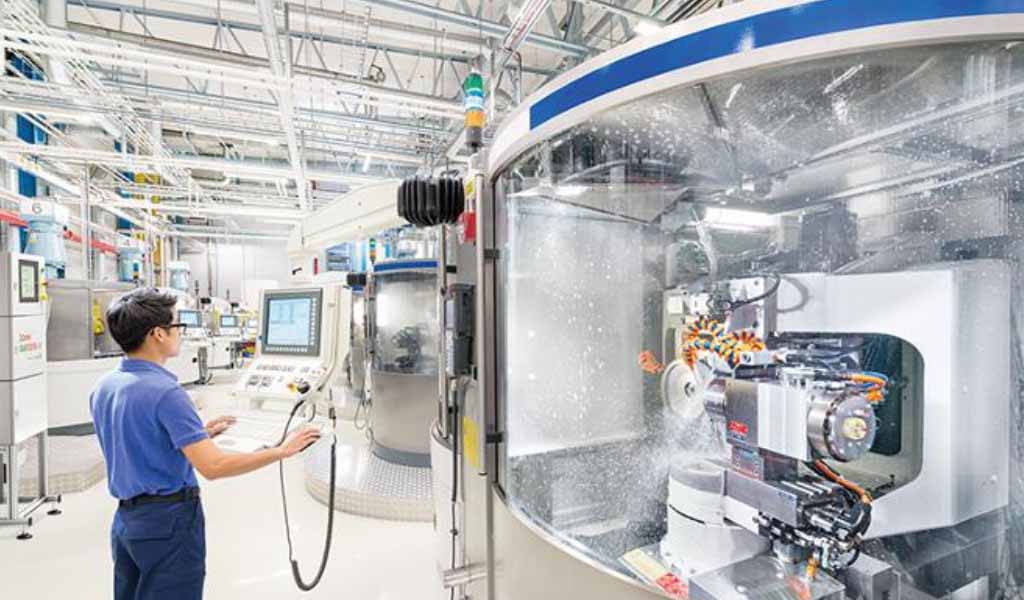
La implementación del concepto Industry 4.0 requiere el uso de una serie de tecnologías facilitadoras fundamentales.
Estos incluyen sensores para la recopilación de datos, redes para la comunicación instantánea de esos datos con la potencia de procesamiento de TI asociada, y su análisis inmediato para crear retroalimentación que pueda optimizar los procesos involucrados en tiempo real y apoyar la programación del mantenimiento predictivo.
No necesariamente se asocian estas tecnologías de vanguardia con el filo literal de las operaciones básicas de mecanizado en taller, en las que las herramientas de alta velocidad en contacto con los metales están continuamente empapadas en fluidos para metalurgia (MWF) para garantizar la lubricación y el enfriamiento.
Sin embargo, la gestión de fluidos para la metalurgia es una actividad de apoyo fundamental en las operaciones de fabricación, con implicaciones directas en la producción, los niveles de eficiencia, la calidad del producto y las condiciones de trabajo.
Los fluidos para metalurgia que se utilizan por debajo de la especificación de concentración mínima pueden producir olores, emulsiones inestables, un rendimiento deficiente y una calidad deficiente, lo que provoca un desperdicio de recursos. La estabilidad de los fluidos puede estar especialmente en riesgo debido a la actividad microbiológica.
Esto crea la necesidad de monitorear los MWF continuamente y tratarlos con aditivos para mantenerlos dentro de las especificaciones. El enfoque tradicional consiste en una mezcla de pruebas manuales y muestreo de laboratorio, que pueden ser costosas y llevar mucho tiempo, además de plantear riesgos para la salud y la seguridad debido a las tareas de drenaje y manipulación de fluidos que implican. Las medidas correctoras consiguientes también serán puramente reactivas.
Riesgos evitados
Un nuevo proceso busca resolver estos problemas aplicando los principios de la Industria 4.0 a los MWF. Castrol SmartControl, de la filial BP, es una solución automatizada de monitorización del estado en tiempo real. Puede "maximizar la eficacia y la eficiencia de la gestión de los fluidos de corte y limitar los riesgos asociados para la salud y la seguridad", según Mathias Buschbeck, líder industrial global de Castrol.
Como explicó Buschbeck, el sistema proporciona monitoreo continuo en tiempo real de la condición del fluido - su pH, concentración, conductividad, temperatura y flujo volumétrico.
Añadió que podría modificarse para que funcionara con otros fluidos. "Puede ser instalado en cualquier sistema central", dijo.
Los usuarios de MWF normalmente operan grandes sistemas centrales de almacenamiento de fluidos conectados a las máquinas herramienta a través de tuberías, con hasta 10 o más máquinas suministradas por una sola fuente.
Buschbeck dijo que el sistema SmartControl está conectado al sistema central a través de un bypass y que debido a que está integrado de esta manera la prueba es un proceso continuo que puede operar 24 horas al día, 7 días a la semana si es necesario.
Conexión en red completa
El sistema mide la concentración de la emulsión de forma totalmente automática con un refractómetro en la operación de bypass, mientras que también se mide el nivel de pH de la emulsión.
Las capacidades técnicas del sistema fueron desarrolladas por el fabricante alemán de equipos mineros Tiefenbach Control Systems. Incluyen la capacidad clave de Industry 4.0 para conectarse en red en sistemas de TI más amplios. "SmartControl puede conectarse a otro sistema a través de una interfaz SQL o wi-fi", dijo Buschbeck. "Los datos también se pueden mover a través de un lápiz de memoria USB."
El hardware básico está alojado en un gabinete simple y compacto que requiere sólo una fuente de alimentación de 220V o 110V para alimentar una unidad de procesador central de 2GHz con 80GB de almacenamiento.
La consecuencia, dijo Buschbeck, es un "sistema de auto-limpieza y auto-calibración que ofrece una automatización completa que puede ser conectada a sistemas de TI más amplios del cliente. El usuario obtiene la información y el sistema añade automáticamente lo que se necesita al MWF".
El sistema ya se está utilizando en la industria. "Se está probando en entornos de fabricación reales, con versiones anteriores en uso durante más de 12 meses", dijo Buschbeck.
"Los resultados son precisos, y los usuarios saben que serán informados si necesitan actuar o cuando el sistema automático actúe en su nombre si es necesario ajustar los niveles".
El sistema ofrece un ejemplo llamativo de cómo, con las aportaciones de los ingenieros tanto del lado del hardware como del del software, Industry 4.0 finalmente está pasando de ser una palabra de moda a ser una herramienta práctica en la planta de producción, y permite que los fluidos que antes se pasaban por alto proporcionen una visión clave del proceso de fabricación.
Fuente: imeche

TAMBIÉN TE PUEDE INTERESAR
Gestión de riesgos geotécnicos en minería subterránea: Prevención . . .
13/Aug/2025 4:35pm
Descubre las herramientas y protocolos clave para prevenir deslizamientos, hundimientos y fallas estructurales en miner . . .
Impulsan la conectividad minera con nuevos corredores de alta capacida . . .
13/Aug/2025 4:32pm
La nueva infraestructura enfocada en corredores mineros en Arequipa permitirá mejorar la calidad y cobertura de los ser . . .
Argentina: Argenta Silver anuncia hallazgo récord de plata de alta le . . .
13/Aug/2025 4:29pm
Argenta Silver Corp. anuncia resultados excepcionales en su proyecto El Quevar, Salta. Se halló plata de alta ley, con . . .
Gobierno lanzará en noviembre plan minero de US$ 250 millones junto a . . .
13/Aug/2025 4:28pm
El programa, que se ejecutará en seis años, busca modernizar trámites, fortalecer la sostenibilidad del sector y acel . . .
Suscríbete al Boletín
Para recibir noticias diarias de Tecnología Minera