Machine Learning como base para el mantenimiento de la Minería 4.0
Publicado hace 2 años
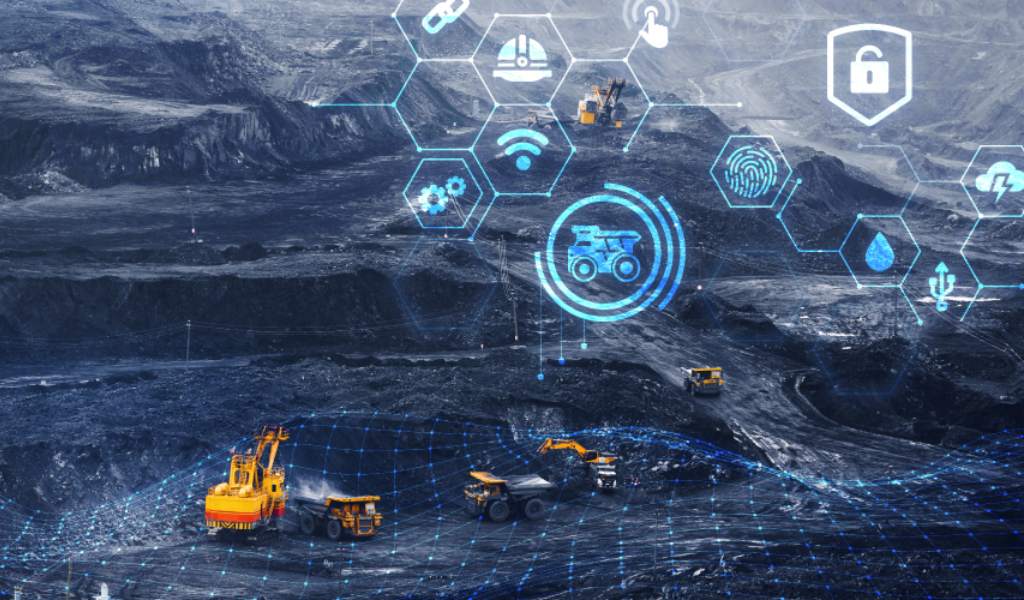
Los avances tecnológicos han conducido a importantes mejoras en el desempeño de las operaciones, obteniendo resultados en la reducción de costos y mejoras en la productividad.
Los avances tecnológicos han conducido a importantes mejoras en el desempeño de las operaciones, obteniendo resultados en la reducción de costos, en mejoras en la productividad y en disminución de tiempos, necesidades de traslado y de plazas presenciales en lugares de alto riesgo.
La necesidad de continuar potenciando la toma de decisiones, en pro de una industria más eficiente, sustentable y segura, genera la exigencia de utilizar la mayor cantidad de información disponible, para así beneficiarse de la historia, las probabilidades y la ciencia de datos, como pilares para la maximización de resultados.
La alta importancia del estado de salud de los activos críticos, la disponibilidad de conocimiento experto en el mercado, el alto impacto en tiempos, costos y seguridad de una detención no planificada, generan una creciente necesidad de encontrar nuevas formas para la evolución en el mantenimiento de plantas. En este punto es donde encontramos el mantenimiento predictivo y su evolución hacia el mantenimiento prescriptivo.
Este modelo se basa en la sinergia generada por el conocimiento experto del fabricante en conjunto con el conocimiento específico de un sitio y su contexto operacional, adicional a los datos de la sensorización existente, las capacidades actuales de las redes IIoT, arquitecturas Cloud y la ciencia de datos, para la construcción de algoritmos de Inteligencia Artificial (IA) en aplicaciones de Machine Learning.
Esto, con el objetivo de predecir posibles fallos futuros y prescribir acciones que permitan evitarlos y/o retrasarlos en pro de generar las planificaciones y adecuaciones necesarias para maximizar los beneficios, dando un paso con esto, hacia el mantenimiento prescriptivo de equipos.
En la actualidad, se han llevado a cabo pruebas aplicadas en chancadores de la empresa alrededor del mundo, con resultados potenciales obtenidos en términos de confiabilidad, disponibilidad, costos y tiempos totales de detenciones no planificadas.
La metodología utilizada para este desarrollo se basa en tomar la data existente desde sensores, el entendimiento del comportamiento físico de un equipo, tanto del fabricante como del personal de terreno, y la comprensión de su matriz de modos de falla y efecto, para crear un set de modelos de alta correlación y causalidad física implementados mediante algoritmos de Inteligencia Artificial basada en aplicaciones de Machine Learning y que de manera conjunta sean capaces de predecir fallas futuras con alta probabilidad de ocurrencia y de manera altamente especifica.
Fuente: Tecnología Minera

TAMBIÉN TE PUEDE INTERESAR
Últimas innovaciones en maquinaria pesada impulsan eficiencia y soste . . .
25/Aug/2025 5:13pm
La maquinaria pesada evoluciona con avances en automatización, digitalización y energías limpias, transformando la pr . . .
LaRonde: Conoce la mina subterránea que construyó Agnico Eagle . . .
25/Aug/2025 5:11pm
A la sombra del cinturón de rocas verdes de Abitibi, en Quebec, justo al oeste de Val-d'Or, se encuentra una mina que c . . .
Chile: Aprueban proyecto para construcción de parque solar por US$ 2 . . .
25/Aug/2025 5:09pm
Se trata del parque fotovoltaico Soles del Norte que considera una potencia instalada de 120 MW, energía equivalente al . . .
Gerentes líderes de empresas mineras globales participarán de PERUMI . . .
25/Aug/2025 5:05pm
PERUMIN 37 la convención minera líder en Latinoamérica y el mundo reunirá a destacados gerentes globales de la indus . . .
Suscríbete al Boletín
Para recibir noticias diarias de Tecnología Minera